«Перші в Союзі», «перші у світі»... Ці фрази наприкінці 50-х років минулого століття часто звучали на адресу української металургії. Наприклад, на одному із запорізьких підприємств уперше було освоєно технологію електрошлакового переплавлення (ЕШП) і розроблено обладнання для її реалізації. Відтоді минуло 55 літ: 28 травня 1958 року на електрометалургійному заводі «Дніпроспецсталь» було отримано перший напівпромисловий злиток методом ЕШП.
У кращі часи збудований спеціально для плавки методом ЕШП п’ятий сталеплавильний цех видавав майже 11—12 тисяч тонн металу. Точну цифру сьогодні назвати не можна, адже у радянський час дані про обсяги виробництва СПЦ-5 були засекреченими. Тут виготовляли сталь для «оборонки».
Зі зникненням Радянського Союзу не стало й замовлень військово-промислового комплексу. Працювати в умовах ринкової конкуренції стало непросто.
Сьогодні СПЦ-5 забезпечує встановлені обсяги виробництва — близько тисячі тонн металу на місяць — для атомної, машинобудівної й інших галузей.
Такою кількістю замовлень може похвалитися небагато металургійних підприємств у країнах СНД, які використовують метод ЕШП. Існує ціла низка галузей, де електрошлакове переплавлення незамінне.
Впровадження у світову практику технології електрошлакового переплавлення по праву вважається одним з головних досягнень української металургії. І важко переоцінити ту роль, яку відіграли в цьому процесі першопрохідники — фахівці «Дніпроспецсталі» та Інституту електрозварювання імені Е. О. Патона.
Так усе починалося
Електрошлакове переплавлення на завод потрапило, якщо можна так сказати, з київського Інституту електрозварювання імені Е. О. Патона. Заводські старожили кажуть, що цей проект був своєрідним котом у мішку, адже пропонували його зварники, а не металурги.
Для проведення дослідів Інститут електрозварювання встановив на «Дніпроспецсталі» (ДСС) майже лабораторну піч
Р-909, щоб на світ з’явився злиток вагою близько 400 кг. Щоправда, відповідно до прийнятих тоді стандартів мінімальна вага промислового заводського злитка становила не менше 700 кг.
Пробні плавки ЕШП, як кажуть, приголомшили: отриманий новим методом метал вирізнявся щільністю й однорідністю, а головне — низьким забрудненням неметалевими включеннями.
Тодішній директор металургійного гіганта — заводу «Дніпроспецсталь» — Олександр Трегубенко мав дивовижну інтуїцію на нові перспективні проекти. Із властивою для нього енергією й наполегливістю він взявся за впровадження нового процесу у виробництво. На базі першого сталеплавильного цеху (СПЦ-1) створили новий структурний підрозділ — вакуумну лабораторію. Тут мали монтувати печі. Правда, було одне «але» — такі печі ще треба було спроектувати, адже на той момент у металургії нічого подібного не робили.
«Проектування відбувалося складно й тяжко, тому що це була перша подібна піч у світі, — згадував у минулому головний механік «Дніпроспецсталі» Віктор Немзер. — Досвіду не було, а сказати, правильно робимо чи ні, було складно. Незабаром кропітка праця проектувальників увінчалася успіхом — проект печі розроблено і передано у виробництво».
У серпні 1961 року розпочинається будівництво нового найбільшого в Європі цеху електрошлакового й вакуумно-дугового переплавлення. Колишню лабораторію на базі СПЦ-1 перейменували на СПЦ-6, потім зробили підрозділом СПЦ-5.
ЕШП забезпечувало найвищу якість конструкційних і нержавіючих, інструментальних і штампових, шарикопідшипникових і теплотривких, долотних і електротехнічних сталей, а також складнолегованих жароміцних сплавів. Але головне — виробництво насправді було економічно вигідним. Саме тому електрошлакове переплавлення почало бурхливо розвиватися в усьому СРСР.
Перед фахівцями Інституту електрозварювання (ІЕС) і «Дніпроспецсталі» було поставлено нове урядове завдання — забезпечити суднобудування, бронетанкову й авіакосмічну галузі високоякісними товстими й тонкими листами. Йшлося про виробництво абсолютно нової продукції — листових злитків масою 10—20 тонн і більше. Необхідно було створити принципово нові технологічні й електричні схеми плавки й управління, зовсім нові печі й допоміжне обладнання. Причому отримати результат треба було в дуже стислий термін.
Уже 1966 року в одному із цехів ДСС запустили 7 печей ЕШП, а через рік — ще 6. Вони були призначені для одержання сортових злитків квадратного перетину масою 2,3 і 4,2 тонни. Цього ж року було запущено першу на заводі піч для виплавки листових злитків масою 10 тонн. А 1968 року побудовано ще дві печі ЕШП і розроблено технологію переплавлення високоміцних конструкційних сталей марок СП28-43 для ракетно-артилерійських систем.
Виробництво постійно зростало, кількість печей збільшувалася. З початку 1970-х років у всіх відкритих документах заводу заборонялося вказувати кількість металу, виготовленого переплавним методом. Але цю інформацію легко було дізнатися завдяки елементарним арифметичним підрахункам. Згідно з відкритими звітними даними всього завод виплавив 1973 року 1 359,4 тис. тонн сталі, а в СПЦ-1, 2 і 3 — 1 268,2 тис. тонн. Таким чином, на СПЦ-5 припадало 91,2 тис. тонн. До речі, це зовсім немале виробництво «делікатесного» металу. У будь-якому разі, у Радянському Союзі більше його ніхто не виготовляв.
Координували роботу академіки Борис Патон і Борис Медовар, а також директори, які очолювали підприємство в 1960—1990 роки: Олександр Трегубенко, Костянтин Єльцов, Микола Стеценко, Геннадій Кійко.
Закордонний досвід
Відповідно до світової практики, технічні й технологічні новинки прийнято продавати на світові ринки. ДСС як власник нової технології допомагала освоювати ЕШП металургам в інших країнах. Одним з учасників цього процесу був у той час старший майстер відділення ЕШП СПЦ-5 Сергій Казаков.
— Звістка про те, що на «Дніпроспецсталі» опановують електрошлакове переплавлення, швидко облетіла металургію по всьому світу. І на завод одна за одною почали приїжджати делегації: із США, Японії, Франції, Англії, Швеції й інших країн. Незабаром було підписано перший контракт — на продаж шведській фірмі «Авеста» електрошлакової біфілярної печі для виплавки злитків до 14 тонн. Слід зазначити, що шведи — великі майстри з виробництва спецсталі, вони славилися цією майстерністю по всьому світу. Однак і вони звернулися до нас із пропозицією продати їм нашу піч ЕШП і технологію.
1970 року до Швеції було направлено групу фахівців від Інституту електрозварювання й «Дніпроспецсталі». Вони мали освоїти близько десяти марок нержавіючої хромонікелевої сталі.
У цьому напрямку одночасно із ДСС активно працювали США й Англія. Так, на фірмі «Лукенз Стіл» (США) було введено в експлуатацію 30-тонну листову піч. В її основу було покладено вже відому одноелектродну схему плавки, що не відповідало високим вимогам ні якості великого листового злитка, ні затрат електроенергії й флюсу. На англійській фірмі «Бритіш Стіл Корпорейшен» теж було введено в експлуатацію піч власного виробництва для листового злитка масою 50 т. В її основу було покладено вже трифазну схему плавки.
Англійським фахівцям не вдалося усунути головний недолік такої схеми — прискорене плавлення центрального електрода і, як наслідок, виникнення макродефектів в осьовій частині злитка. А от біфілярна схема плавки, розроблена радянськими фахівцями, не мала зазначених недоліків і забезпечувала найвищу якість товстого листа ЕШП. Тому саме нашою технологією зацікавилися фахівці японської фірми «Ніппон Стіл Корпорейшн» (НСК) — одного з найбільших світових виробників стали.
В 1971 році фірма НСК влаштувала тендер на створення комплексу ЕШП для виробництва листових злитків масою до 40 тонн. Фахівцям «Дніпроспецсталі» вдалося довести переваги біфілярної схеми порівняно зі схемами, які використовували фірми «Лукенз Стіл», «Бритіш Стіл Корпорейшен», австрійська «Інтеко» і деякі інші великі виробники печей ЕШП.
У цей період в Інституті електрозварювання й на ДСС розпочалася ціла епопея. Японці не один раз бували на ДСС і в ІЕС, детально цікавлячись усім, що пов’язане з виробництвом листових злитків. Адже на той час найбільший листовий злиток на ДСС мав масу лише 13 т, а було потрібно освоїти виробництво злитка масою 40 т.
— Технічний ризик був великим, — каже вчений секретар ДСС Сергій Казаков. — Однак японці після успішної демонстрації плавки в СПЦ-5 повірили нам. Незабаром було підписано ліцензійну угоду на розробку проекту печі й технології ЕШП злитків масою до 40 т (піч ЕШП-40) для фірми НСК.
Роботи з ЕШП-40 розпочалися на ДСС і в ІЕС в 1971 році. Ця піч у всьому відрізнялася від своїх попередників. І досі дивуєшся, наскільки оперативно фахівці ДСС і ІЕС виготовили дослідний короткий кристалізатор, піддон та інше обладнання. Виконали також реконструкцію печі У-436 під нове обладнання й почали роботи з освоєння нової технології. Працювали по 10—15 годин, часто — у нічні зміни...
.jpg)
На знімку: п ’ятий сталеплавильний цех, заливання шлаку в піч ЕШП. 25 травня 1972 року.
За заслуги
За освоєння й розвиток переплавних процесів директор заводу Олександр Трегубенко отримав звання «Лауреат Ленінської премії». Лауреатами Державної премії СРСР у різні роки стали директор заводу Костянтин Єльцов і старший майстер вакуумного відділу цеху Ігор Трегубенко. 1977 року за роботу з освоєння виробництва товстого листа ЕШП групі фахівців, у тому числі Сергію Казакову й Олексію Богаченку, було присвоєно Державну премію УРСР. Нагороди вручав президент НАН України й голова комітету з премій академік Борис Патон.
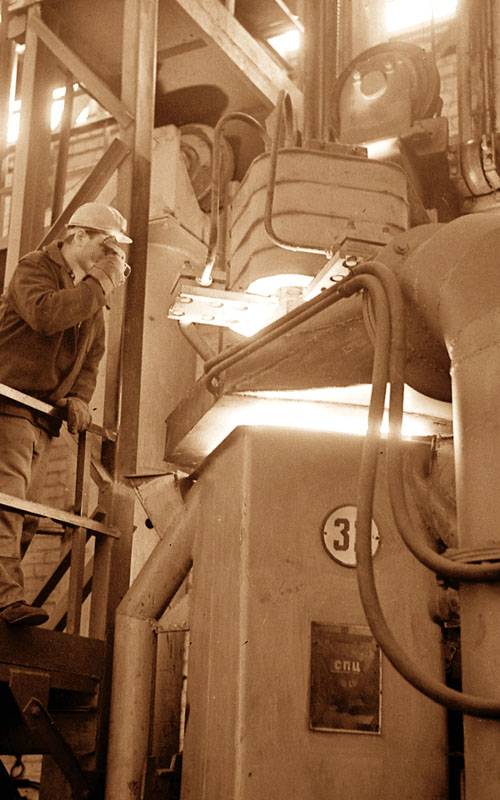
П’ятий сталеплавильний цех. 1969 рік.
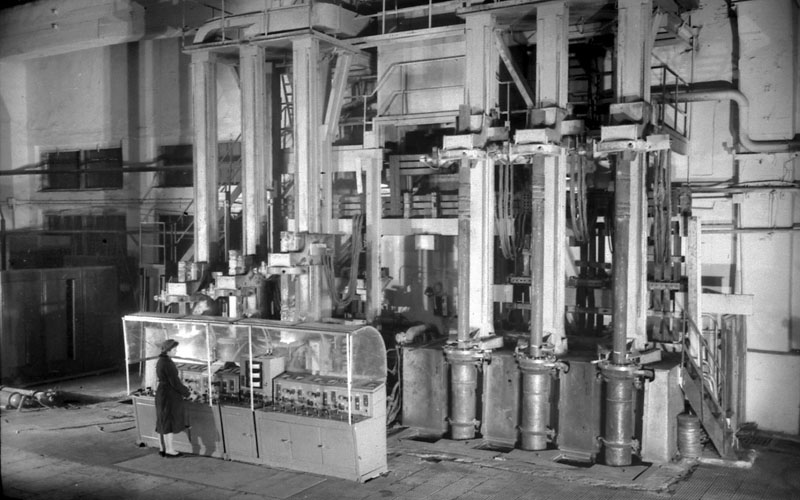
Перші установки ЕШП на заводі «Дніпроспецсталь».
Фото надане ПАТ «Дніпроспецсталь» та музеєм ПАТ «Дніпроспецсталь».